The availability and accessibility of Energy Meter Spare Parts are critical factors that significantly impact the maintenance and longevity of energy metering systems. Energy meters play a vital role in accurately measuring and recording electricity consumption, making them essential components for utility companies and end-users alike. Ensuring a steady supply of spare parts is essential to maintain the accuracy, reliability, and efficiency of these meters throughout their lifecycle. This question delves into the challenges faced by manufacturers and utility companies in managing spare parts and the strategies they can adopt to guarantee a continuous supply and enhance customer satisfaction.
Importance of Spare Parts Availability: Energy meters are designed to have long lifespans, often ranging from 10 to 20 years or more. During this extended service life, it is inevitable that certain components may wear out or fail due to normal wear and tear. The unavailability of essential spare parts can lead to prolonged downtime, inaccurate readings, and potential revenue losses for utility companies. Moreover, end-users may face inconvenience, leading to dissatisfaction with the utility service provider.
Obsolescence and Technological Advancements: With rapidly advancing technology, older energy meters and their spare parts may become obsolete over time. Manufacturers may discontinue certain models to introduce more advanced metering systems with improved functionalities. As a result, ensuring a continuous supply of spare parts for older models becomes a challenge, and utility companies may need to transition to newer systems to address this issue.
Supplier Dependence and Inventory Management: Energy meter manufacturers often rely on a network of suppliers to provide components for their products. Maintaining a stable and reliable supplier base is crucial to ensure a consistent supply of spare parts. Effective inventory management practices are essential to prevent stockouts or excessive inventory of spare parts.
Regulatory Compliance and Certification: Energy meters are subject to various regulatory standards and certifications to ensure accuracy, safety, and compliance with industry guidelines. The availability of certified spare parts becomes vital to maintain the integrity of these metering systems and adhere to regulatory requirements.
Strategies for Ensuring Steady Supply of Energy Meter Spare Parts:
Long-term Planning and Product Lifecycle Management: Manufacturers should incorporate long-term planning and product lifecycle management in their operations. Proactive forecasting and assessment of the demand for spare parts can help manufacturers anticipate requirements and manage inventory accordingly.
Component Standardization and Commonality: Standardizing components across different models of energy meters can facilitate spare parts interchangeability. Commonality in components can simplify manufacturing and inventory management, ensuring that spare parts are readily available.
Collaboration with Suppliers and Partners: Establishing strong collaborations with reliable suppliers is crucial to secure a steady supply of spare parts. Long-term contracts and mutual commitments can ensure that suppliers prioritize the manufacturer's requirements.
Reverse Engineering and Third-party Sourcing: For older or obsolete models, manufacturers may explore the option of reverse engineering or sourcing spare parts from third-party vendors. This can help extend the lifecycle of existing energy metering systems and support utility companies in maintaining their metering infrastructure.
Regular Updates and Upgrades: Encouraging utility companies to regularly update and upgrade their energy metering systems to newer models can mitigate the challenges of spare parts availability for older models. Incentives and support for upgrades can be provided to facilitate this transition.
Collaboration with Utility Companies: Utility companies can collaborate with manufacturers to establish spare parts management programs. Regular communication and feedback from utility companies can help manufacturers understand specific needs and plan spare parts production accordingly.
Proactive Spare Parts Inventory Management: Utility companies can adopt proactive spare parts inventory management practices, such as forecasting usage, establishing reorder points, and maintaining buffer stocks to ensure timely availability of spare parts when needed.
In conclusion, the availability and accessibility of Energy Meter Spare Parts significantly impact the maintenance and longevity of energy metering systems. Manufacturers and utility companies need to adopt proactive strategies, such as long-term planning, standardization, collaboration with suppliers, and proactive inventory management, to ensure a steady supply of spare parts and enhance customer satisfaction. By addressing the challenges of spare parts availability, the industry can uphold the accuracy, reliability, and efficiency of energy metering systems, meeting the needs of both utility companies and end-users.
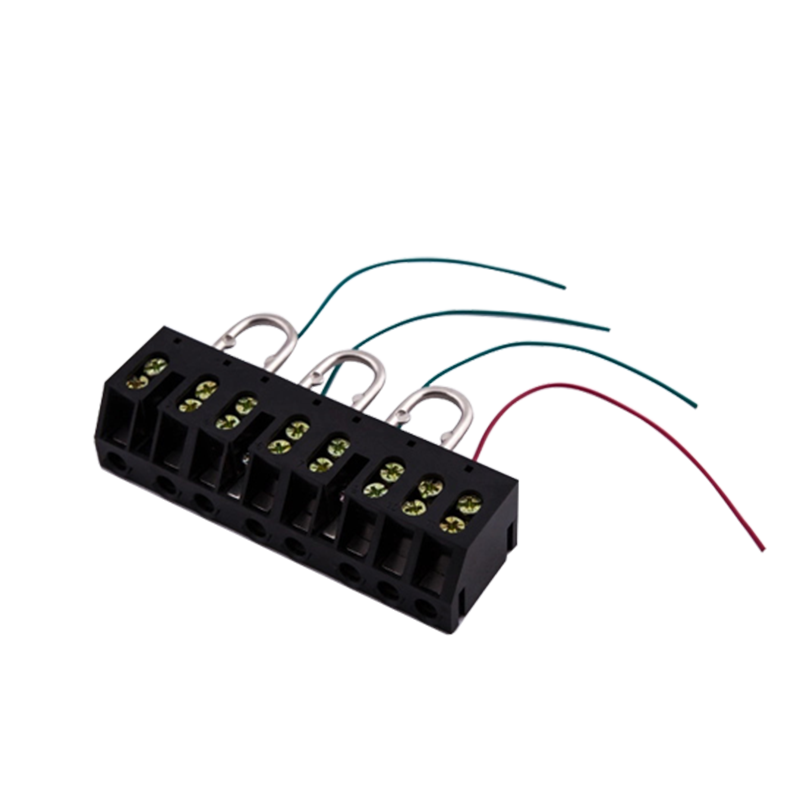
RS485 CE Contactor For Remote Electrical Circuit Control And Measurement
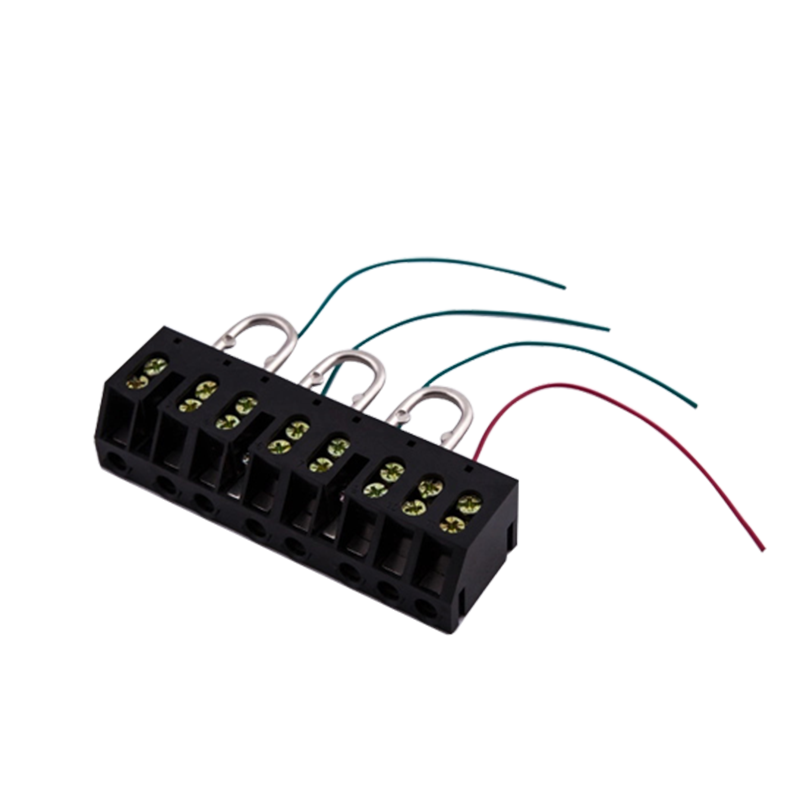
RS485 CE Contactor For Remote Electrical Circuit Control And Measurement